consulTATION
Simulation Services
-SIMULATION SERVICES-
SAFER - STRONGER - FASTER
WITH BETTER RELIABILITY
Simulation Services - By utilizing powerful computer simulation software, designs can be virtually tested and optimized. This allows designs to be iterated upon in much shorter time and with less expense than building and testing prototypes.
ABOUT SIMULATION
Our computer simulation services allow products and machines to be developed faster and with less development cost. Our simulation software is fully integrated with our CAD modeling programs, allowing seamless iterative designs, parametric optimization, side-by-side design comparison, and more.
FINITE ELEMENT ANALYSIS
FEA (Finite Element Analysis) is used to simulate internal stresses within solid parts. By simulating external loads, the design geometry can be optimized to:
-
Reduce weight
-
Increase fatigue life
-
Increase strength
-
Study distortion and deflection
-
Study effects of various materials
​
With our FEA software, we can model external loads such as forces, pressures, centrifugal forces, buckling, and heat input. We can also study harmonics and natural frequencies of your design. In cases where thermal expansion may be of concern, we can model multi-physics simulations, combining physical loads and heat input.
​
Some examples of where FEA can be used:
-
Structural/beam analysis
-
Shaft design
-
Deflections due to loading
-
Factor of Safety (FoS)
-
Failure analysis and redesign
COMPUTATIONAL FLUID DYNAMICS
CFD (Computational Fluid Dynamics) is used to simulate fluids and heat transfer within or around a design. Our advanced CFD software can simulate:
-
Static and transient fluid flow
-
Rotating reference frames
-
Fluid to Solid or Fluid to Fluid heat transfer
-
Boundary layers
-
Turbulence/Flow streamlines
-
Cavitation
-
Porous media
-
Convection, Conduction, and Radiation
-
Particle studies
-
Sub-Sonic and Super-Sonic flow < M5.0
-
Surface roughness effects
​
With advanced CFD simulation capabilities, we can model complex multi-physics fluid flow analyses. By understanding the thermal and mechanical phenomena occurring within a design, optimization may be carried out. Some examples of where CFD can be used:
-
Mass/Volume flow rates
-
Fluid velocity
-
Heatsinks
-
Electronics cooling
-
Fluid mixing
-
Fluid flow optimization
-
Fans/Pumps
-
Surface erosion caused by particulates or cavitation
-
Particle evacuation/accumulation
-
Heat exchangers
HEAT TRANSFER ANALYSIS
Utilizing our FEA or CFD software, steady state and transient heat transfer simulations can be modeled accurately and efficiently. Focusing on heat transfer, we can simulate:
-
Heat flow through solids and fluids
-
Effects of contact resistances
-
Forced and passive heatsinks
-
Heat exchangers
-
Electronics cooling
-
Thermoelectric coolers
-
Heating/cooling elements
Native Support For:
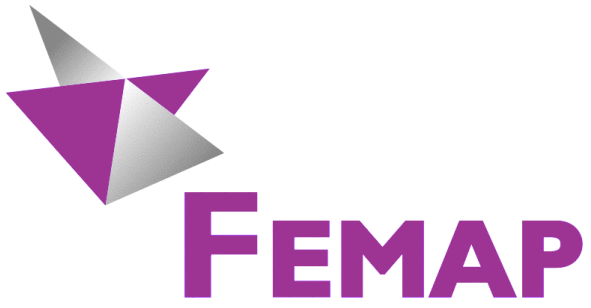

-
FEA Analysis
-
Modal Analysis
-
FEA + Heat Transfer Analysis
-
CFD Analysis
-
Heat Transfer Analysis
-
CFD + Heat Transfer Analysis